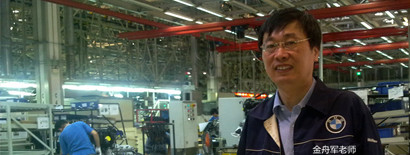
精益生产培训企业咨询、培训-企业内部培训和机构合作请咨询
精益生产培训公开课--培训地点:江苏无锡万达广场 满四人开班 小班教学 每月开班
—金舟军老师 手机/微信:13816949004 QQ邮箱:923503608@qq.com
以应用为导向培训,学员培训后就会应用,金舟军培训咨询质量保证流程确保顾客满意。
请点击查看—金舟军培训咨询质量保证流程
精益生产管理咨询培训
精益生产培训公开课讲师汽车质量专家金舟军,机构上海企业管理咨询有限公司,是汽车制造行业专业、实战的培训,包括汽车制造行业消除七种浪费、节拍生产、单件流、防错应用等,精益生产培训班和企业内训请垂询,考试合格发放精益生产培训证书,合格权威精益生产证书。
必须找金老师精益生产管理培训的理由
1.专业的精益生产培训咨询讲师
金老师二十年专业从事汽车制造行业IATF16949及精益生产培训咨询课程,每个培训项目的客户都有培训现场的视频和照片为证。
2.实战的精益生产培训
金舟军老师不仅追求良好的课堂培训效果,更追求精益生产培训咨询课程后学员的实战应用,金老师在培训前首先要进行网络、电话的沟通和提前一天到顾客现场调研,更好地结合顾客的案例讲课,安排学员对案例的演练。
3.有价值的精益生产培训咨询公司
2.实战的精益生产培训
金舟军老师不仅追求良好的课堂培训效果,更追求精益生产培训咨询课程后学员的实战应用,金老师在培训前首先要进行网络、电话的沟通和提前一天到顾客现场调研,更好地结合顾客的案例讲课,安排学员对案例的演练。
3.有价值的精益生产培训咨询公司
咨询公司金老师自办,省出了业务费用和老板利润,客户的培训费全部变为培训老师的培训费,,客户培训价值最大化值。
金舟军汽车制造行业培训客户
上海延锋韦世通、苏州德国大陆、常熟伟速达上海德尔福、武汉东风汽车、江苏东风起亚、江苏麦格纳、安微江淮汽车、、湖北武汉佛吉亚、上海奥托立夫、重庆长安汽车、沈阳宝马汽车、上海德尔福汽车空调、辽宁大连固特异轮胎、长春大众集团、湖北武汉佛吉亚、上汽集团、吉林一汽集团、广西上汽通用五菱、广西玉林重工、江西长力股份 北京北汽福田广州木桥、福建新能源科技、湖南三一重工、苏州恩斯克轴承、辽宁曙光汽车、武汉哈金森、苏州力特奥维斯、重庆 嘉陵集团 福建奔驰汽车、辽宁大连大众变速箱 广东广州中博、上海奥托立夫 广东深圳比亚迪 河南新乡豫新 河北莱尼、浙江华远、山东莱尼 、山东胜地、武汉哈金森、上海科世达
金舟军汽车制造行业培训客户
上海延锋韦世通、苏州德国大陆、常熟伟速达上海德尔福、武汉东风汽车、江苏东风起亚、江苏麦格纳、安微江淮汽车、、湖北武汉佛吉亚、上海奥托立夫、重庆长安汽车、沈阳宝马汽车、上海德尔福汽车空调、辽宁大连固特异轮胎、长春大众集团、湖北武汉佛吉亚、上汽集团、吉林一汽集团、广西上汽通用五菱、广西玉林重工、江西长力股份 北京北汽福田广州木桥、福建新能源科技、湖南三一重工、苏州恩斯克轴承、辽宁曙光汽车、武汉哈金森、苏州力特奥维斯、重庆 嘉陵集团 福建奔驰汽车、辽宁大连大众变速箱 广东广州中博、上海奥托立夫 广东深圳比亚迪 河南新乡豫新 河北莱尼、浙江华远、山东莱尼 、山东胜地、武汉哈金森、上海科世达
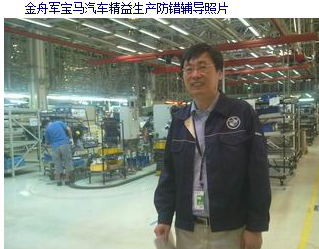
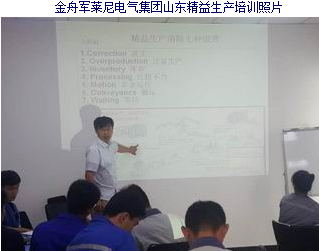
结合客户案例的实战型培训 包括后服务答疑的全过程
金舟军老师通过五大步骤结合客户案例讲解,确保学员学完全就会在工作中应用: 1 .案例网络调研、2.案例学员预习、3. 现场案例调研、4.案例练习点评、5.售后案例答疑。
1.案例网络调研
培训意向一经确定,金舟军老师就要与客户进行网络沟通,确定精益生产实施难点,收集精益生产实施资料,并就实施资料的细节进行沟通,并了解客户学习精益生产的目的。
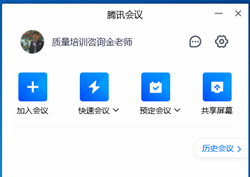
2.学员案例预习
金舟军老师根据精益生产实施中的难点,事先为学员出精益生产的预习题,帮助学员提前思考怎样解决实施案例的难点,同时也预习课堂讲解的知识。
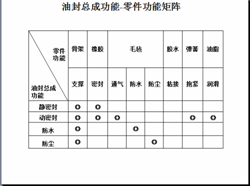
3. 现场案例调研
培训前一天,金舟军老师会到客户现场进行一天的现场调研,查找客户精益生产实施情况,并为课堂针对客户实施精益生产中的问题讲解做准备。
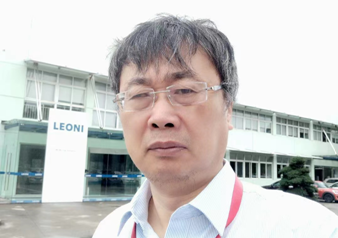
4.案例练习点评
根据案例实施中的难点问题,每天培训约有五十分钟的客户案例分组练习,每组学员的案例练习金舟军老师都要做详细的点评,确保学员学完全就会在工作中应用。
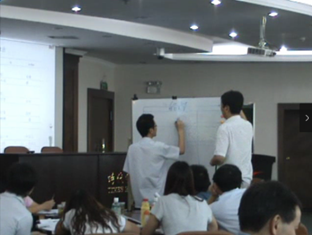
5.售后案例答疑
培训完成后一年之内,如果客户在实施精益生产过程中有什么问题,可以为客户组织腾讯会议的在线答疑至少三次
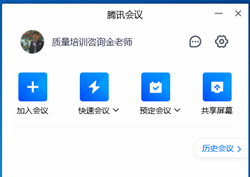
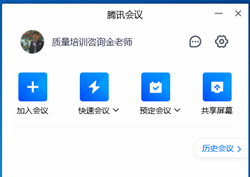
精益生产管理培训公开课培训班
课程公开课大纲--本大纲为简版课程大纲,需要更详细课程大纲请索取
一.精益生产培训目的:通过学习,学员能掌握精益生产的方法,并能利用拉动式准时化生产、目视管理、看板管理、价值流分析、流线生产线布置等方法消除企业中的七种浪费。
二.精益生产培训对象:生产管理、质量管理、现场管理人员和班组长。
三.精益生产课程内容
1部分.精益生产产生和发展背景汽车质量网版权
当今两种生产方式优劣比较
案例演练-TPS丰田生产方式有哪些优点
2部分.精益生产原理
实施精益生产的生产现场基础
案例演练-精益生产包括哪几个方面
3部分.实施精益生产消除七种浪费方法
浪费的定义MUDA和消除
案例演练-什么是浪费MUDA
4部分.精益思想的五个基本原则
判断生产有价值的原则
案例演练-拉动原则实施包括舟哪些内容
5部分.实施柔性生产方法 汽车质量网版权
滅小制造周期时间的方法
案例演练有哪些措施减小通过时间
6部分.实施过程风险分析方法
生产过程风险发生率评价
案例演练-基于什么指标评价生产过程过程风险发生率
7部分.实施价值流分析方法
怎样消除公开的浪费的过程
案例演练-生产过程价值流分析价值时间由哪些因素决定的
8部分.作业切换时间方法
怎样减少快速换模时间
案例演练-有哪些措施减小生产过程外部切换时间
9部分.实施单件流方法
流水线无停顿和堵塞的生产流程 汽车质量网版权
案例演练-工艺顺布置CELL的原则有哪些
10部分.实施节拍生产方法
用户节拍决定工厂的脉搏
案例演练-怎样调整产品生产工序循环时间
11部分.实施拉动生产方法
看板数量计算方法
案例演练-生产过程看板至少应包括哪些内容
12部分.实施自働化方法 汽车质量网版权
三种检验方法与零缺陷
案例演练-为什么说自働化就是防错的一种实施形式
13部分.实施零缺陷方法
过程质量决定产品质量
两种零缺陷指标及其实现方法
怎样提高首次通过率
案例演练-首次通过率为什么要排除返工产品的数量
14部分.实施防错方法达到零缺陷
三种类型防错方法汽车质量网版权
动作步骤探测防错法
案例演练-防止钻孔位置不合格触碰式防错法的应用
15部分.实施透明工厂的方法
目视化每日/周/月维护
案例演练-设计一个生产目视化版面
16部分.实施TPM全面设备维护方法达到零缺陷
提高OEE设备综合效率的方法
案例演练-设计一个设备清扫清单
17.实施持续改进
持续改进的方法 汽车质量网版权
案例演练-纠正措施与纠正的区别是什么
18部分实施管理人员现场负责
出现在距创造价值近的地方
案例演练-经理办公室需要搬到现场吗
19部分..人员标准化作业方法
标准作业步骤或要素
案例演练-怎样划分标准作业步骤,要考虑哪些因素
20部分.实施零浪费策略
减少浪费是持久的挑战.
案例演练-为什么要员工参与编制作业指导书.
21部分.现场实施定置管理方法
工艺研究确定物流布置 汽车质量网版权
案例讨论-编制某一工序工位布置图
22部分5S实施精益生产的基础
整理整顿清扫清洁素养
案例演练-编制某一工序清扫清单
四.精益生产课程学时:每天6.5小时共2-8天
柔性-通过时间
降低通过时间会导致过程的柔性和高度的顾客导向。暂短的准备时间,可以随时在短时间内更换产品型号。
通过时间
企业的生产流程包括:订单处理、物料计划、采购下单、供应商备料、运输、来料检验、存储、搬运、加工、检验
和返工、过程等待、成品库存、发运、货款回收等环节
过程价值流分析
价值只能由最终用户来确定。
价值流中在价值流中找到增值的过程、不增值的浪费过程,识别浪费和消灭浪费。
价值流程图ValueStreamMapping
VSM价值流程图是丰田精益生产系统中用来描述物流和信息流的形象化工具,价值流包括增值活动和非增值活动,对生产制造过程中的周期时间、待机时间、在制品库存、原材料流动、信息流动等情况进行记录,目的是为了辨识和减少非增值活动。
信息流从客户订单到生产计划的过程;实物流程从原材料、制造、成品入库,直至产品送达客户。
作业切换时间
生产流水线需要变换产品品种,涉及到作业切换的时间,两种品种间的间隔即为作业切换时间。
很多切换是可以在设备运转时进行的,可实际上却在停机时进行。
内部切换时间:设备必须停下来进行的作业切换,模具、刀具和工装夹具等的切换。
外部切换时间:设备运转当中进行切换,流水线的换线只需要将新的产品送生产线。
快速换模SMED
SingleMinuteExchangeofDies
新乡重夫50年代在日本丰田公司发展起来的SMED最初是应用在汽车行业,切换时间由4小时缩短为3分钟。
一种能有效缩短切换时间的方法,以最小的设备停机时间来进行不同产品间的生产切换,最大限度提高设备利用率的方法。
作业切换时间
将内部作业切换时间转换为外部作业切换时间。
缩短内部作业切换时间。
缩短内部作业切换时间。
课程公开课大纲--本大纲为简版课程大纲,需要更详细课程大纲请索取
一.精益生产培训目的:通过学习,学员能掌握精益生产的方法,并能利用拉动式准时化生产、目视管理、看板管理、价值流分析、流线生产线布置等方法消除企业中的七种浪费。
二.精益生产培训对象:生产管理、质量管理、现场管理人员和班组长。
三.精益生产课程内容
1部分.精益生产产生和发展背景汽车质量网版权
当今两种生产方式优劣比较
案例演练-TPS丰田生产方式有哪些优点
2部分.精益生产原理
实施精益生产的生产现场基础
案例演练-精益生产包括哪几个方面
3部分.实施精益生产消除七种浪费方法
浪费的定义MUDA和消除
案例演练-什么是浪费MUDA
4部分.精益思想的五个基本原则
判断生产有价值的原则
案例演练-拉动原则实施包括舟哪些内容
5部分.实施柔性生产方法 汽车质量网版权
滅小制造周期时间的方法
案例演练有哪些措施减小通过时间
6部分.实施过程风险分析方法
生产过程风险发生率评价
案例演练-基于什么指标评价生产过程过程风险发生率
7部分.实施价值流分析方法
怎样消除公开的浪费的过程
案例演练-生产过程价值流分析价值时间由哪些因素决定的
8部分.作业切换时间方法
怎样减少快速换模时间
案例演练-有哪些措施减小生产过程外部切换时间
9部分.实施单件流方法
流水线无停顿和堵塞的生产流程 汽车质量网版权
案例演练-工艺顺布置CELL的原则有哪些
10部分.实施节拍生产方法
用户节拍决定工厂的脉搏
案例演练-怎样调整产品生产工序循环时间
11部分.实施拉动生产方法
看板数量计算方法
案例演练-生产过程看板至少应包括哪些内容
12部分.实施自働化方法 汽车质量网版权
三种检验方法与零缺陷
案例演练-为什么说自働化就是防错的一种实施形式
13部分.实施零缺陷方法
过程质量决定产品质量
两种零缺陷指标及其实现方法
怎样提高首次通过率
案例演练-首次通过率为什么要排除返工产品的数量
14部分.实施防错方法达到零缺陷
三种类型防错方法汽车质量网版权
动作步骤探测防错法
案例演练-防止钻孔位置不合格触碰式防错法的应用
15部分.实施透明工厂的方法
目视化每日/周/月维护
案例演练-设计一个生产目视化版面
16部分.实施TPM全面设备维护方法达到零缺陷
提高OEE设备综合效率的方法
案例演练-设计一个设备清扫清单
17.实施持续改进
持续改进的方法 汽车质量网版权
案例演练-纠正措施与纠正的区别是什么
18部分实施管理人员现场负责
出现在距创造价值近的地方
案例演练-经理办公室需要搬到现场吗
19部分..人员标准化作业方法
标准作业步骤或要素
案例演练-怎样划分标准作业步骤,要考虑哪些因素
20部分.实施零浪费策略
减少浪费是持久的挑战.
案例演练-为什么要员工参与编制作业指导书.
21部分.现场实施定置管理方法
工艺研究确定物流布置 汽车质量网版权
案例讨论-编制某一工序工位布置图
22部分5S实施精益生产的基础
整理整顿清扫清洁素养
案例演练-编制某一工序清扫清单
四.精益生产课程学时:每天6.5小时共2-8天
柔性-通过时间
降低通过时间会导致过程的柔性和高度的顾客导向。暂短的准备时间,可以随时在短时间内更换产品型号。
通过时间
企业的生产流程包括:订单处理、物料计划、采购下单、供应商备料、运输、来料检验、存储、搬运、加工、检验
和返工、过程等待、成品库存、发运、货款回收等环节
过程价值流分析
价值只能由最终用户来确定。
价值流中在价值流中找到增值的过程、不增值的浪费过程,识别浪费和消灭浪费。
价值流程图ValueStreamMapping
VSM价值流程图是丰田精益生产系统中用来描述物流和信息流的形象化工具,价值流包括增值活动和非增值活动,对生产制造过程中的周期时间、待机时间、在制品库存、原材料流动、信息流动等情况进行记录,目的是为了辨识和减少非增值活动。
信息流从客户订单到生产计划的过程;实物流程从原材料、制造、成品入库,直至产品送达客户。
作业切换时间
生产流水线需要变换产品品种,涉及到作业切换的时间,两种品种间的间隔即为作业切换时间。
很多切换是可以在设备运转时进行的,可实际上却在停机时进行。
内部切换时间:设备必须停下来进行的作业切换,模具、刀具和工装夹具等的切换。
外部切换时间:设备运转当中进行切换,流水线的换线只需要将新的产品送生产线。
快速换模SMED
SingleMinuteExchangeofDies
新乡重夫50年代在日本丰田公司发展起来的SMED最初是应用在汽车行业,切换时间由4小时缩短为3分钟。
一种能有效缩短切换时间的方法,以最小的设备停机时间来进行不同产品间的生产切换,最大限度提高设备利用率的方法。
作业切换时间
将内部作业切换时间转换为外部作业切换时间。
缩短内部作业切换时间。
缩短内部作业切换时间。
缩短调整作业。